9 Consejos para mejorar la calidad del agregado de arena y grava
El agregado de arena y grava es el componente más básico del concreto y juega un papel importante en la construcción de concreto. Acerca de 1.5 Se requieren medidores cúbicos de arena y agregado de grava para cada metro cúbico de concreto. Por lo tanto, La calidad del agregado de arena y grava afecta la calidad del proyecto hasta cierto punto.
Con la construcción de infraestructura como carreteras, ferrocarril, y casas, La demanda del mercado de agregados de arena y grava está aumentando. La producción de agregados de arena y grava de alta calidad también se ha vuelto más importante. Este artículo compartirá algunos consejos que pueden mejorar la calidad de los agregados de arena y grava..
1.Seleccionando la roca principal adecuada
La calidad del agregado de arena y grava debe controlarse desde la selección de materias primas para producir productos terminados que cumplan con los requisitos.
En primer lugar, La calidad de la roca principal afecta directamente la calidad de la arena artificial.. Por lo tanto, Seleccionar rock parental calificado es un paso muy importante. La roca matriz necesita seleccionar la roca principal que ha pasado la prueba de radiactividad y el experimento de reacción de agregados alcalinos.
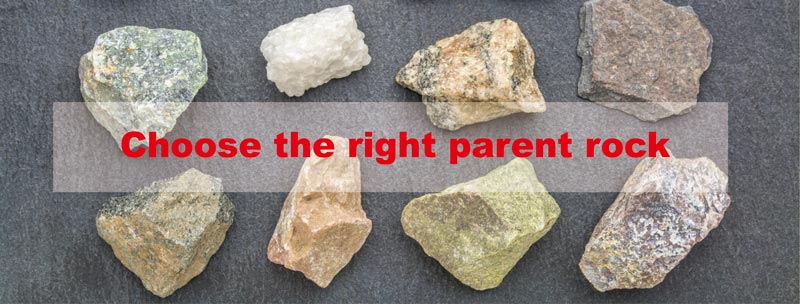
En segundo lugar, Seleccione la piedra caliza, dolomita y otras rocas parentales con dureza media y bajo contenido de sílice. Entonces, Elija rocas parentales duras y frágiles como granito y toba. No elija rocas parentales con alta resistencia y resistencia a la compresión como basalto y cuarcita como materiales de alimentación.
Finalmente, Trate de elegir la roca padre con menos impurezas como el suelo y la materia ligera.
El trabajo del control de calidad de la minería de materia prima consiste en la limpieza de sobrecarga y la carga de materia prima. Después de que se borre la sobrecarga, será confirmado por el ingeniero geológico, y luego se llevará a cabo la minería de materia prima. Las materias primas procesadas son inspeccionadas directamente por inspectores de calidad a tiempo completo, y las materias primas que están gravemente resistidas o tienen muchos escombros o barro se tratan como desechos, y la calidad de las materias primas se controla activamente desde la fuente de producción.
Métodos de minería de roca para padres
Minería superficial: Este es un método de minería común y se aplica a depósitos abiertos o afloramientos de roca. Eliminación de la roca principal de las áreas mineras de superficie mediante la explosión, Equipo de excavación y transporte.
Perforación y voladura: Este método se usa cuando los bloques más grandes de la roca principal deben romperse. Se perfora un agujero a través de la roca principal por medio de una máquina de perforación y se coloca una carga de explosión en el agujero. Entonces, La droga se detonará para dividir la roca principal en trozos manejables.
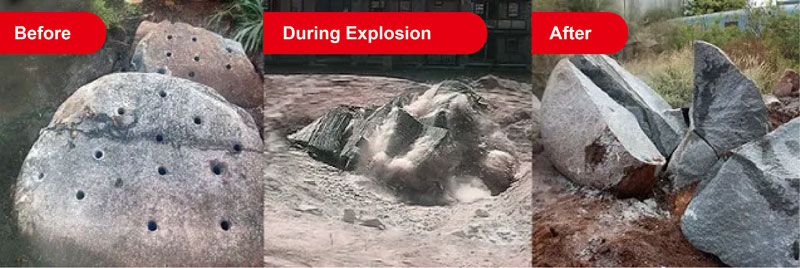
Método de corte: Este método es adecuado para rocas más duras, como granito. La roca principal es cortada por equipos mecánicos, como cortadores de rocas, cuchillas de sierra, etc..
Método de túnel: Este método se usa a menudo en la minería subterránea y es adecuado para roca parentada profunda enterrada. Excavando rampas o túneles, se accede al depósito subterráneo y se extrae la Madre Rock.
2.Elija el equipo de fabricación de arena adecuado
De acuerdo con las características climáticas locales y las características de la roca matriz, Intente elegir el proceso de procesamiento en seco y el equipo de trituración rentable.
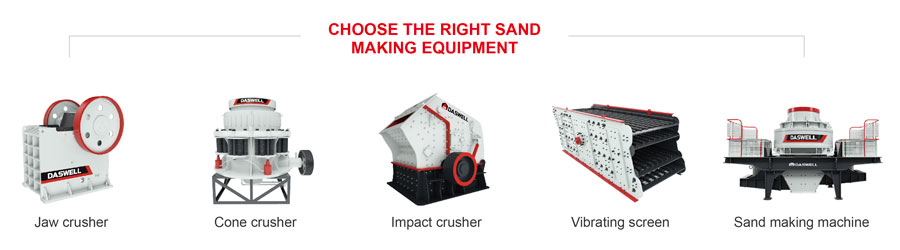
Para materiales de forma media como piedra caliza, Se pueden usar trituradoras de impacto en lugar de trituradoras de martillo. Esto se debe a que los agregados procesados por la trituradora de martillo tienen contenido de escamas de aguja alta, muchas grietas oscuras dentro del agregado, Valor de aplastamiento bajo, y alto valor de pérdida de solidez.
Para materiales duros como rocas como granito, Se usa una trituradora de cono de múltiples cilindros con función de trituración laminada para un triturador fino, que puede reducir el contenido de escamas en forma de aguja de los agregados de arena y grava y reducir la presión de la configuración agregada posterior.
3.Eliminar el suelo antes del triturador grueso
Porque las materias primas de roca matriz se mezclan con el suelo, rocas desgastadas de piel de montaña, etc., Estas impurezas con baja resistencia a la compresión son generalmente pequeñas en tamaño de partícula. Antes de triturar grueso, La combinación de alimentador de barras y tamiz de eliminación del suelo se usa para prescindir de las impurezas para mejorar la calidad de la arena y el agregado de grava terminados.
4.Elija el equipo de detección adecuado y el separador de polvo fino
La carga de detección de la pantalla vibratoria debe ser moderada, y se deben usar más de dos capas de máquinas de detección. Y la pantalla debe estar en forma de agujeros cuadrados tanto como sea posible, y el tamaño de malla apropiado debe determinarse.
La fabricación de arena seca debe elegir un separador de polvo fino o un colector de polvo con función de regulación de la velocidad de conversión de frecuencia, que puede ajustar el contenido de polvo de piedra en la arena terminada. La fabricación de arena húmeda debe elegir una lavadora de arena adecuada, y el consumo de agua y la velocidad del tornillo en la lavadora de arena deberían ser razonables.
5.Adoptar el modo de fabricación de arena seca
(1) Cuando se usa como arena artificial para la producción de concreto de alto rendimiento o mortero mixto seco, La roca matriz debe usarse sobre la base de cumplir con los requisitos. La materia prima también debe ser restos de piedra o piedra de arroz limpia con tamaño de partícula de 5-15 mm después de la remoción del suelo y el polvo fino, y el sistema de fabricación de arena de la estación de construcción debe usarse en la medida de lo posible.
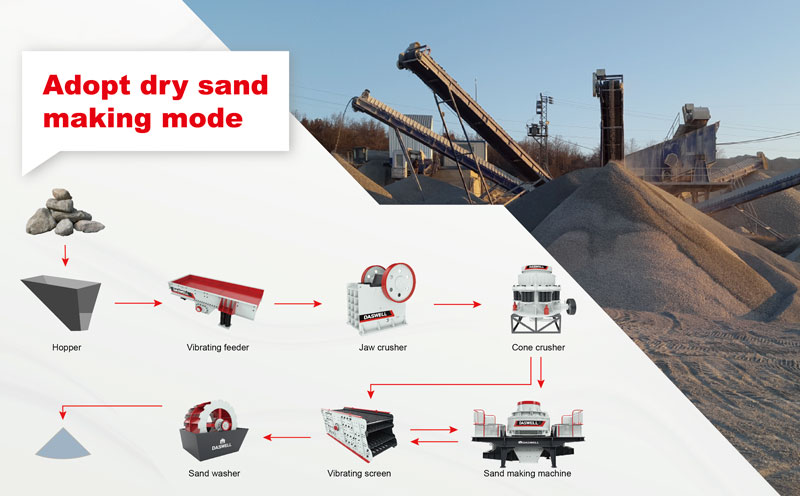
(2) Cuando la arena terminada se use como materia prima de la planta de mezcla de concreto, El contenido de humedad de la roca principal debe ser menor que 3%, y el contenido del suelo debería ser menor que 1%. Cuando la arena terminada se use como materia prima para mortero mezclado en seco, La humedad y el contenido de suelo de la roca parental deberían ser menores que 1%, Para garantizar que el contenido de humedad de la arena hecha a máquina no seca terminada sea menor que 0.5%.
(3) Cuando la máquina de fabricación de arena y el sistema de detección de polvo fino existen al mismo tiempo, ajustar razonablemente la proporción del 4.75-2.36 parte de la partícula mm en la arena terminada. El exceso de parte se devuelve a la máquina de fabricación de arena para hacer arena circulante.
Según los diferentes usos de la arena de alta calidad, Ajuste el contenido de polvo de piedra en la arena terminada, acerca de 3%-10%, Para cumplir con los requisitos de gradación de tamaño de partícula de arena de alta calidad hecha a máquina.
6.Resolver el problema del revestimiento en polvo
En el proceso de producción agregada, Las medidas de lavado se toman principalmente para resolver el problema del recubrimiento en polvo de los agregados. Se instala una válvula de regulación en la tubería de lavado para controlar el volumen de agua de lavado de acuerdo con la condición del material bruto y para garantizar que la presión del agua de lavado sea de 24.5 a 29.4 Pensilvania.
7.Control del diámetro excesivo y bajo diámetro
En el proceso de producción agregada, El control del sobre diámetro y el diámetro inferior es principalmente para cumplir con los requisitos de la clasificación agregada al aumentar la frecuencia de la inspección agregada y ajustar el ancho de la abertura de procesamiento. Las principales medidas son:
(1) para agregado grueso, Es necesario instalar un dispositivo de velocidad al final de la máquina en la correa de descarga para evitar que el agregado sea aplastado y separado de la gradación agregada debido a una gran caída.
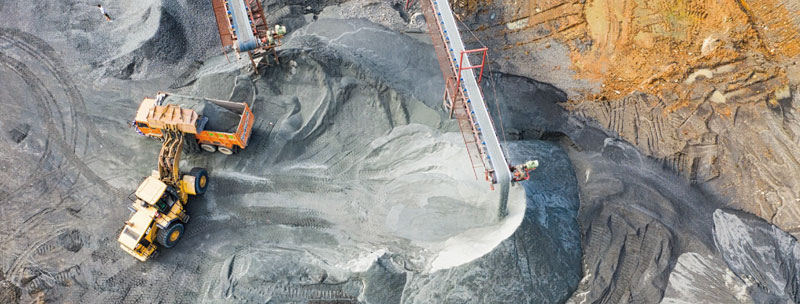
(2) Se establece una pared de separación entre varios agregados terminados para evitar mezclar entre agregados de gran tamaño y de menor tamaño.
(3) Elija una apertura de pantalla razonable, Verifique la pantalla una vez que cada ciclo de trabajo, y reemplácelo a tiempo de acuerdo con la condición de desgaste.
(4) Los materiales de stock de varios contenedores de productos terminados se dan regularmente y se usan, y los contenedores se eliminan a tiempo para evitar la acumulación de materiales rotos y materiales en polvo.
(5) Cuando el vehículo de transporte agregado está cargando, El material debe tomarse uniformemente, no a lo largo de la periferia del material, Para evitar la separación del agregado causado por la carga.
8.Controlar el contenido del agregado de escamas de aguja
El control del contenido del agregado de escamas de aguja es principalmente a través de la selección de equipos. Debido a la diferente composición mineral y estructura de varias rocas, La forma del grano y la gradación de la roca después del trituración no son las mismas.
El contenido de los materiales de escamas de aguja producidas por diferentes trituradoras es diferente. Las trituradoras de la mandíbula producen agregados con contenido de escamas de aguja ligeramente más alto que las trituradoras giratorias y las trituradoras de cono. Las trituradoras de impacto producen agregados con un contenido de escamas de aguja inferior.
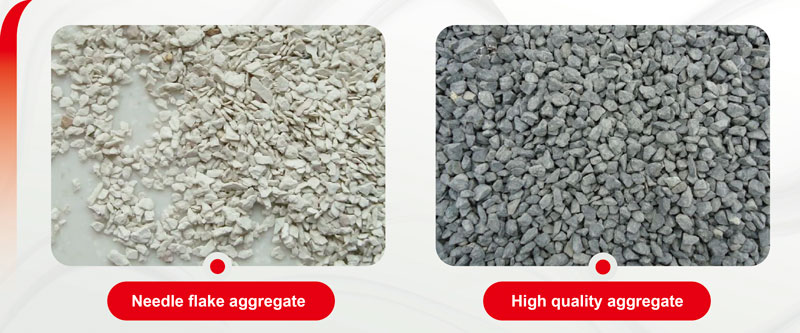
9.Instale el equipo para probar la calidad de la arena hecha a máquina
Para garantizar la estabilidad de la calidad de la arena hecha a máquina, Se instala un dispositivo de detección en línea en la exportación de productos terminados para detectar la calidad de la arena hecha a máquina en tiempo real y realizar redes inalámbricas para monitoreo remoto. Cuando se encuentra que la calidad del agregado no cumple con los requisitos, realizar inmediatamente una consulta, proponer una solución, ajustar el equipo, y complete la capacidad de control de la calidad agregada.
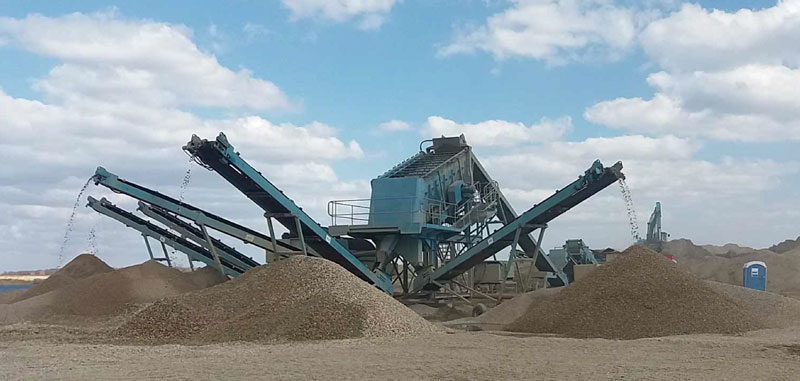
La arena hecha a máquina está reemplazando gradualmente la arena natural y ampliamente utilizada en proyectos de construcción de ingeniería. Elija Materias primas adecuadas de arena y grava, Considere completamente los posibles factores de influencia, como contenido agregado similar a una aguja, contenido de lodo, Contenido de humedad y contenido de polvo de piedra, etc., y aumentar continuamente el control de calidad de producción para mejorar la calidad de producción de los agregados de arena y grava para garantizar la calidad general de los proyectos de ingeniería.